Robus India is the foremost producers of Automatic Die Cutter machines in India.
Excellence Series’ 1060AT
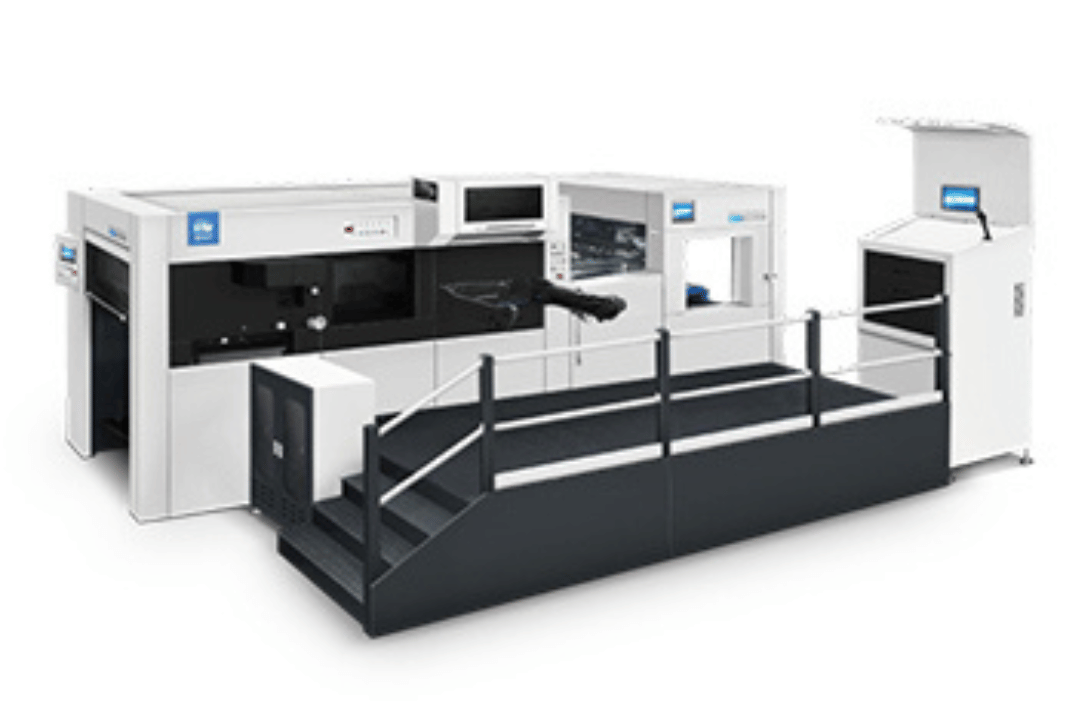
- Expertise Jobs with 600 Tons Cutting Pressure & Heating Chase – Cake base cutting, kappa board cutting, puzzle job cutting, micro-embossing, nano/deep embossing, 3D embossing and plastic job with soft creasing.
- Comprehensive Foil Feeding – Longitudinal and lateral hot foil stamping at the same time, reducing the foil usage and saving foil replaced time.
- Foil Control – Such as foil advancing step combination setting, automatic most efficient stepping combination calculation as well as motion stepping combination simulation and, hologram stamping is of the latest technology the foil control system and provides reliable and precision foil advancing control.
- Waste Foil Rewinding Unit – Outside the delivery section controlled by the foil control system for efficient waste foil rejection and keeping foil tension constant by synchronizing the waste foil pulling with foil advancing.
- Variable Speed Worm Gear Drive Device – Allows large motion angle hence minimum number and size of nicks at reasonable max production speed.
Key Features:
Technical Specification:
Key Features:
Feeder:
- Three lifting up and four forwarding sucker heads with angle adjustment to handle different kind of materials.
- Preloading device with rail cart and scaled gate.
- Manually side adjustment of pallet table (+/- 40 mm).
- Side adjustment of pallet table.
- Non-stop feeder with automatic pile lift.
- Side blowers adjustable according to sheet size for smooth feeding, especially for smooth thin paper transport.
Feeding Table:
- Left and right-side push lays to ensure accurate alignment and power registration.
- Sheet slows down device of feeder belts to assure accurate position of the sheet to the front lays (electro-pneumatically adjustable).
- Synchronizing device to adjust the sheet positioning to the front lay by hand during production.
- Feed table inlet equipped with lateral ramps.
- Four individually adjustable front lays at the operation side of the machine.
- Ultra-sonic double sheet detector (without contact).
- Sheet hold-down device (guiding the sheets to the front lays).
- Upper frame with manual lifting device.
- Pull and push convertible side lays (OS and OOS) with photo sensor sheet arrival control.
Die-Cutting Section:
- Precision worm gear crank toggle driving system to ensure smooth and dynamic lower platen movement.
- Short stroke movable platen, driven by eccentric worm gear and toggle mechanism allows large motion angle hence minimum number and size of nicks at reasonable max. Production speed.
- Precision stationery upper platen.
- State-of-Art 3 cam index gripper bar drive system to ensure smooth and precise gripper bar intermittent movement.
- Pneumatic clutch/brake for main drive system.
- Motorized cutting force setting by push button.
- Digital strain gauge die cutting pressure tonnage display at HMI with adjustable pressure limit protection.
- Eight high precision alloy gripper bars.
- High quality pre-stretched gripper bar drive chain.
- Torque limit safety clutch to protect the index drive system in case of gripper bar crash.
- Double cam driven gripper opener and front lay swing frame without position restore spring for smooth and accurate sheet register and take off.
- Pneumatic push button die chase locking mechanism to ensure safe and operator friendly changing of the die.
- 5mm hardened cutting plate or 4+1mm sandwich plate (optional) on top of 15mm precision synthetic supporting plate with +/-0.9mm micro adjustment for quick set up and make ready.
- Automatic main chain lubrication system.
Hot Stamping Section:
- Man-machine interactive touch function, can set different long pull and short pull.
- The alarm will be triggered when the foil is shorter than 6cm.
- The computer deals with foil monitoring system, used to display remaining and have used foil length.
- Comprehensive foil feeding system, can realized longitudinal and lateral hot foil stamping at the same time, reducing the foil usage and saving foil replaced time.
- Three sets of longitudinal foil advancing shafts and two sets of lateral foil advancing shafts are driven by servo motors individually programmable for short and long foil stepping.
- Foil feeding devices are controlled by servo motor and siemens PLC control system.
- Foil breaking control.
- Tension roller and foil advancing rollers each driven servo motors and controlled by the foil control system, new pressing roller on tension roller with easy pressure adjustment hence quick set up.
- Foil control, such as foil advancing step combination setting, automatic most efficient stepping combination calculation as well as motion stepping combination simulation and, hologram stamping is of the latest technology the foil control system and provides reliable and precision foil advancing control.
- Waste foil rewinding unit outside the delivery section controlled by the foil control system for efficient waste foil rejection and keeping foil tension constant by synchronizing the waste foil pulling with foil advancing.
Delivery Section:
- Automatic paper aligning device and two blowers for paper collection can ensure neat collection of thin and thick papers.
- Air blowers to press down the sheets.
- Rear and side joggers with easy position adjustment.
- Gripper edge stripping and removing system with conveyor or belt to remove the gripper edge waste sideways to the drive system.
Electrical Control Panel:
- Adopts electrical components of world-famous brands for better performance and in time and local after-sale-service and maintenance.
- Latest PLC technology to ensue safe and trouble free running.
Technical Specification:
MODEL | BHT – 1060AT |
Max. Sheet Size | 1060 X 760 mm |
Min. Sheet Size | 400 X 350 mm |
Max. Die Cutting Size | 1060 X 745 mm |
Min. Gripper Margin | 9-17 mm |
Stock Range | 90~2000 g/m² (Card Paper) |
≥ 4 mm (Corrugated Paper) | |
Die Cutting Accuracy | ± 0.075 mm |
Max. Cutting Pressure | 600 Tons |
Machine Speed | 8000 S/H |
Feeder Pile Height | 1630 mm (Including Wooden Pallet) |
Delivery Pile Height | 1580 mm (Including Wooden Pallet) |
Max. Foil Diameter | Longitudinal – 250 mm |
Lateral – 200 mm | |
Foil Width | 20 – 1020 mm |
Electric Heating System | 12 Temperature Zones 40-180 Degree Adjustable |
Main Motor Power | 15 Kw |
Total Power Required | 56 Kw |
Machine Dimensions (Length: Including Pre-Feeding Track, Width: Including the Pedal) | 8000 X 4518 X 2762 mm |
Total Weight of Machine | 24 Tons |
Air Pump Displacement | 0.6~0.7Mpa, ≥0.37m3/min |
Technical Specification:
SMODEL | BHT – 1060AT |
---|---|
Max. Sheet Size | 1060 X 760 mm |
Min. Sheet Size | 400 X 350 mm |
Max. Die Cutting Size | 1060 X 745 mm |
Min. Gripper Margin | 9-17 mm |
Stock Range | 90~2000 g/m² (Card Paper) ≥ 4 mm (Corrugated Paper) |
Die Cutting Accuracy | ± 0.075 mm |
Max. Cutting Pressure | 600 Tons |
Machine Speed | 8000 S/H |
Feeder Pile Height | 1630 mm (Including Wooden Pallet) |
Delivery Pile Height | 1580 mm (Including Wooden Pallet) |
Max. Foil Diameter | Longitudinal – 250 mm Lateral – 200 mm |
Foil Width | 20 – 1020 mm |
Electric Heating System | 12 Temperature Zones 40-180 Degree Adjustable |
Main Motor Power | 15 Kw |
Total Power Required | 56 Kw |
Machine Dimensions (Length: Including Pre-Feeding Track, Width: Including the Pedal) | 8000 X 4518 X 2762 mm |
Total Weight of Machine | 24 Tons |
Air Pump Displacement | 0.6~0.7Mpa, ≥0.37m3/min |
We are Here to Serve You, Reach us Now
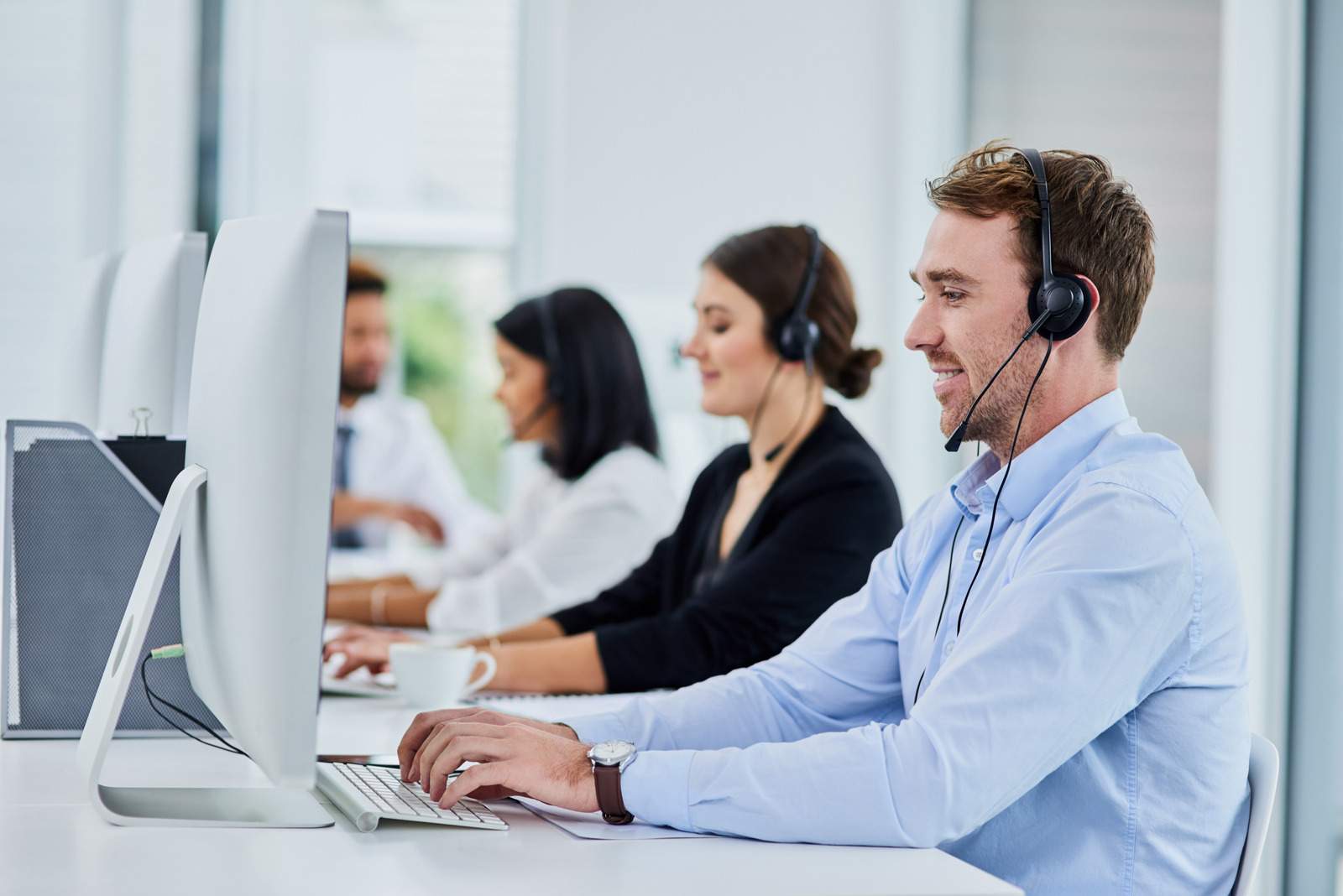
Related Products
Robus India is the foremost producers of Automatic Die Cutter machines in India.